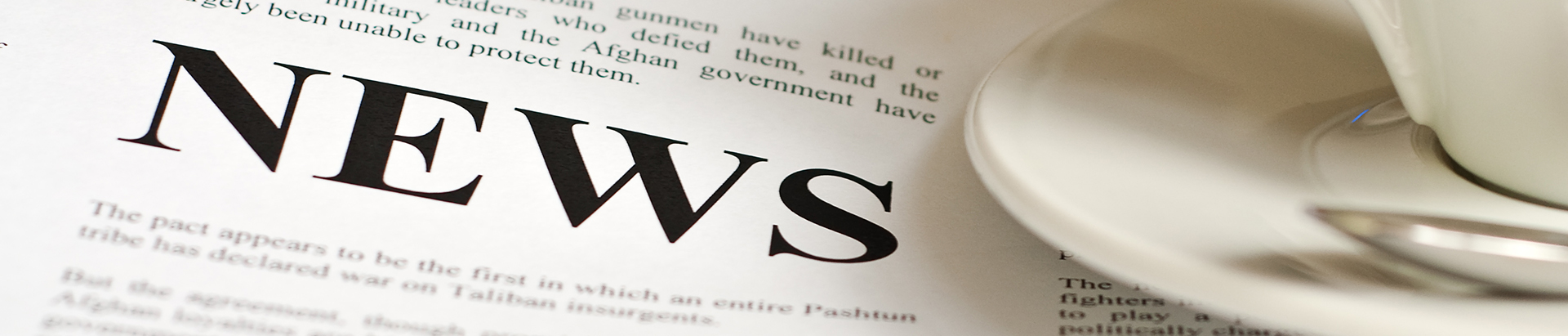
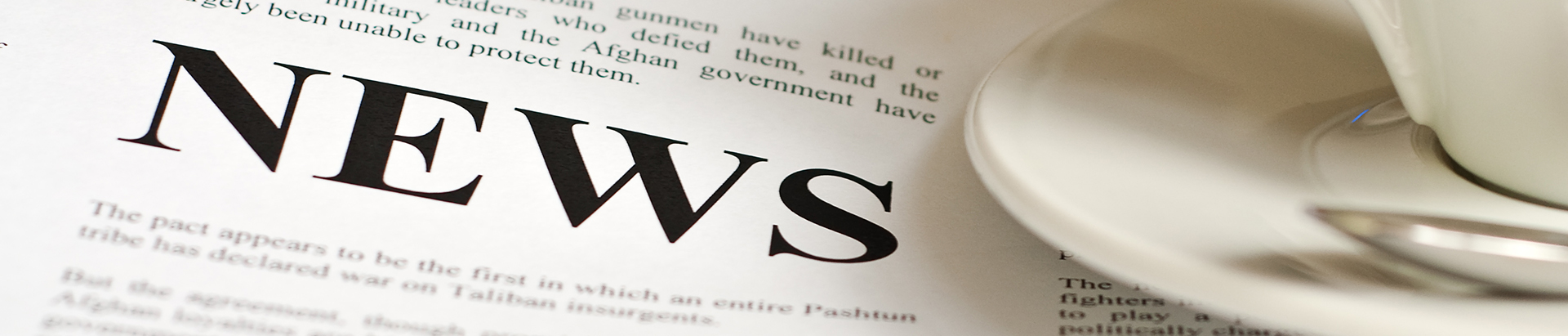
With the explosive growth of AI model training and inference demands, the thermal management of high-power-density servers is facing unprecedented challenges. When the power of a GPU cluster exceeds 20kW per cabinet, the cooling efficiency of traditional air-cooling systems approaches its physical limit. Liquid cooling technology, with its more than hundredfold increase in heat dissipation capacity per unit volume, is becoming the core support for AI computing infrastructure.
In practical applications of liquid cooling systems, the precision of flow control directly impacts cooling efficiency and system safety. The industry currently faces three major technical challenges:
1. Imbalance in Dynamic Flow Matching
In scenarios where server workloads fluctuate drastically, a fixed flow rate model can lead to localized hotspots.Rapid GPU core temperature spikes may result in computation throttling or even hardware damage.
2. Energy Efficiency Bottleneck
Over-provisioning of flow rates to handle peak cooling demands results in over 30% of pump power consumption waste. Increased system pressure may heighten the risk of pipeline leaks.
3. Multi-Physics Interference Issues
The viscosity of coolant varies with temperature, causing flow measurement drift. High-frequency vibrations can distort sensor signals, compromising long-term monitoring stability.
ADW’s Advanced Flow Sensors for AI Liquid Cooling
To tackle these challenges, ADW has introduced a dedicated AI server liquid cooling flow sensor series, built specifically for AI liquid cooling systems. This series integrates ultrasonic and vortex flow sensing technologies, establishing a full-chain flow monitoring system from chip-level cooling to cabinet-level thermal management.
With ±3% measurement accuracy and millisecond-level response speed, these sensors dynamically balance energy efficiency and cooling performance.
Principle: Based on the time-difference method, measuring the time delay of ultrasonic waves traveling with and against the coolant flow.
Key Benefits:
- High-precision interference-free liquid flow monitoring
- Integrated real-time control in AI server liquid cooling systems
- Ensures efficient GPU/CPU cooling even under overclocking workloads
Principle: Uses the Kármán vortex street effect, detecting vortex frequency as coolant passes through the vortex generator.
Key Benefits:
- Suitable for high-flow, high-speed, and high-viscosity coolants
- Real-time stable flow measurement using fluid dynamics models and signal processing
- Dynamic coolant flow adjustment to sustain high-performance computing stability
These cutting-edge sensors enable AI data centers to maintain optimal thermal management, reducing energy waste and safeguarding hardware performance under extreme workloads.