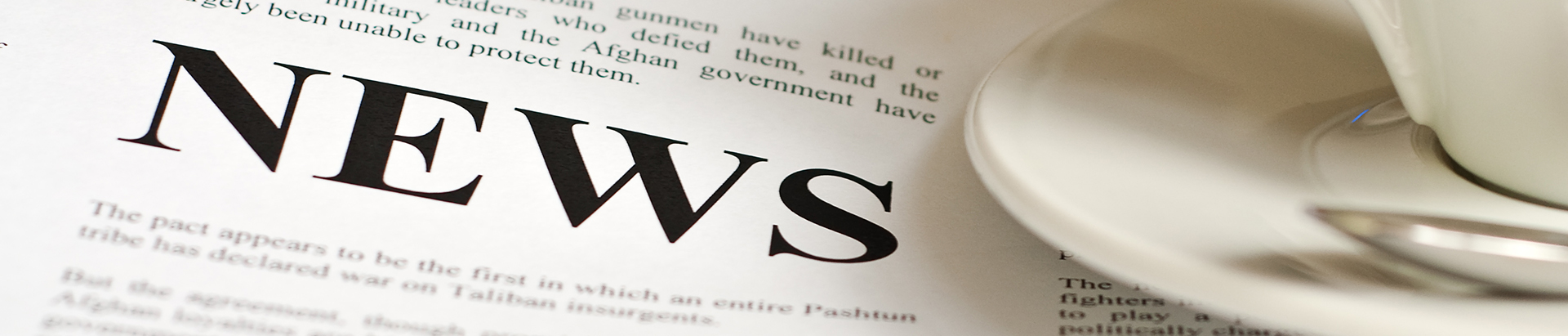
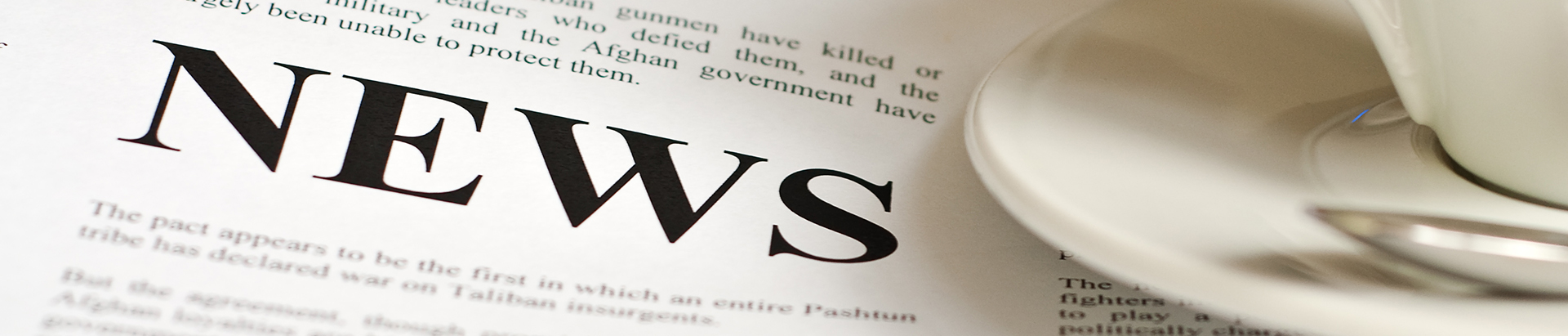
In today’s rapidly advancing technological landscape, AI has become a driving force for transformation across industries. From large-scale servers in data centers to everyday smart devices, AI equipment is ubiquitous. However, as AI devices become increasingly powerful, heat dissipation challenges are growing. Precise control of coolant flow is crucial to ensuring stable operation, and vortex flow sensors play an indispensable role in this process.
Early flow measurement devices, such as orifice plate flow meters, calculated flow rates by measuring the pressure difference as fluid passed through a restriction. While this method was simple, it had limited accuracy and caused significant interference with fluid flow. The development of ultrasonic technology led to the introduction of ultrasonic flow meters, which measure velocity based on ultrasonic wave propagation in the fluid. These meters offered non-contact measurement with higher accuracy but still had limitations in complex working conditions. The emergence of vortex flow sensors has overcome many of these traditional flow measurement challenges.
Vortex flow sensors operate based on the Kármán vortex street effect. When a fluid, such as coolant, flows through the sensor’s bluff body, alternating vortices are generated downstream. The frequency at which these vortices shed is directly proportional to the fluid velocity. Detection elements inside the sensor capture the tiny pressure fluctuations or vibrations caused by the vortices and convert them into electrical signals. By analyzing these signals and incorporating ultrasonic calibration techniques, the exact coolant flow rate can be accurately determined.
AI equipment cooling systems require high precision, stability, and rapid response. AI chips are highly sensitive to temperature changes, and even minor fluctuations can impact computing performance. This necessitates precise coolant flow control to keep chips operating at optimal temperatures. Furthermore, AI workloads frequently fluctuate—from low-power standby modes to high-intensity computational tasks—demanding a dynamic cooling system that can rapidly adjust flow rates to match varying conditions.
Vortex flow sensors offer exceptional measurement accuracy, detecting even the smallest changes in coolant flow. In AI chip cooling, this precise flow control minimizes temperature fluctuations, enhancing computational efficiency and system stability.
With no moving parts, vortex flow sensors are highly resistant to mechanical wear and corrosion, ensuring outstanding long-term stability. AI equipment often operates continuously for extended periods, and vortex flow sensors significantly reduce maintenance and calibration costs.
Vortex flow sensors can detect flow changes within milliseconds. When AI workloads suddenly increase, the sensor swiftly detects shifts in coolant demand and promptly relays this data to the control system. This ensures timely coolant delivery, preventing overheating.
Whether the system uses water-based or specialized coolants, vortex flow sensors provide accurate measurements. Additionally, they are compatible with various pipeline materials and installation environments, making them highly adaptable to different AI cooling system designs.
With their high precision, stability, rapid response, and adaptability, vortex flow sensors are the ultimate solution for AI equipment coolant flow measurement, ensuring efficient heat dissipation and stable operation in the ever-evolving world of AI technology.