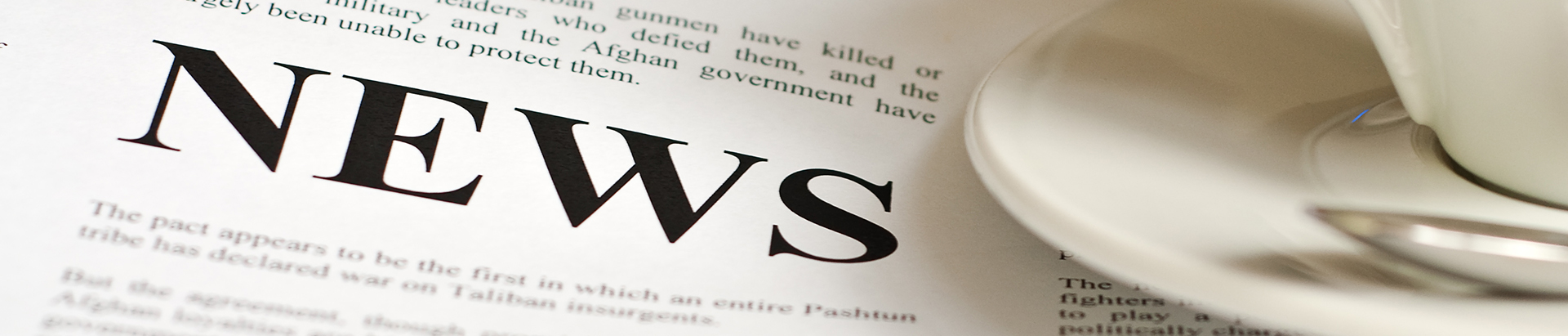
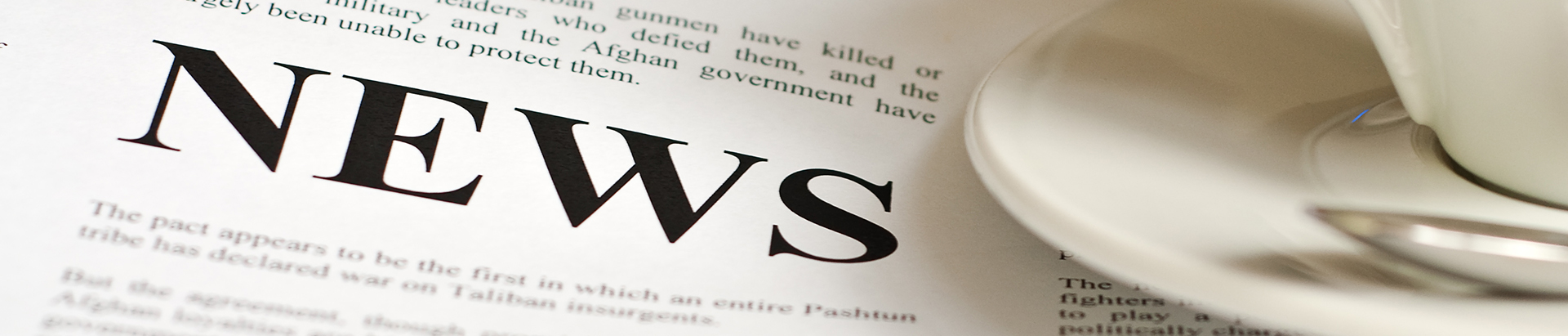
In today’s rapidly evolving technological landscape, AI equipment has become a driving force behind advancements across various industries. However, did you know that these powerful AI devices generate massive amounts of heat during operation? Without proper cooling, their performance can significantly degrade, or worse, they may malfunction. This is where coolant circulation plays a crucial role in maintaining stable operation, and precise coolant flow measurement relies on vortex flow sensors.
Core components of AI devices, such as high-performance chips and processors, generate extreme heat during operation. Take AI servers in large data centers as an example—under continuous high-load computation, chip temperatures can soar into dangerous ranges. The coolant circulation system functions as an "air conditioner" for these devices, constantly transferring heat away to maintain optimal temperatures. However, if the coolant flow is unstable or inaccurately measured, cooling efficiency is compromised, leading to performance degradation and reduced device lifespan. This makes precise coolant flow control essential.
The vortex flow sensor operates on the unique Kármán vortex street principle. When fluid passes through a non-streamlined bluff body (vortex generator) within the sensor, two alternating rows of vortices are generated downstream—this phenomenon is known as the Kármán vortex street. According to ultrasonic fluid measurement theory, the vortex shedding frequency is directly proportional to the fluid velocity. By detecting the vortex frequency, the sensor accurately calculates fluid velocity, which, combined with the pipe’s cross-sectional area, determines coolant flow rate. This non-contact measurement method avoids interference with the fluid, ensuring high accuracy and stability.
Precision is crucial in AI equipment coolant flow measurement. Vortex flow sensors provide exceptional accuracy, with minimal error margins, ensuring the optimal amount of coolant is delivered for stable device operation. For AI chips, which are highly temperature-sensitive, precise flow control maintains ideal working temperatures, enhancing performance and longevity.
AI equipment operates under varying conditions—sometimes requiring low coolant flow for basic cooling, and other times demanding high flow rates for intensive computations. Vortex flow sensors feature a wide turndown ratio, allowing accurate measurement across different flow ranges. Whether handling minimal or large coolant flows, these sensors ensure precise metering to accommodate diverse operational needs.
With no moving parts, vortex flow sensors minimize mechanical wear and reduce failure rates, offering outstanding stability and reliability. In AI systems that run continuously, these sensors require minimal maintenance and calibration, significantly lowering maintenance costs and downtime while improving operational efficiency.
When AI devices undergo sudden changes in workload, their coolant flow requirements shift instantly. Vortex flow sensors respond swiftly, providing accurate real-time flow adjustments to ensure the cooling system adapts efficiently, keeping AI equipment in optimal thermal conditions at all times.
Thanks to their unique working principle and outstanding characteristics, vortex flow sensors play an irreplaceable role in AI equipment coolant flow measurement. As AI technology continues to evolve, the demand for advanced cooling and flow control solutions will increase. Vortex flow sensors will keep innovating, offering even stronger support for the stable operation of AI equipment.